The Problem Emerges (2002-2003)
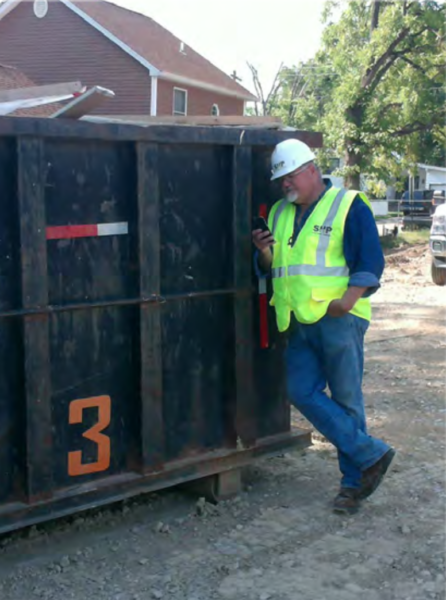
The story of Frame Frog begins in 2002-2003 at a 300,000 square foot Ohio school project with 600 doors, 58 of which required electrification. Gary Johnson, the assigned field representative for an architectural firm, found himself drawing upon all of years as a construction superintendent to rise to what would become a defining professional challenge.
“I had never had any access control before that point,” Gary recalls. “As architects and engineers, we didn’t really have this nailed down about who did what.”
The fundamental problem was immediately apparent: while door hardware was specified in schedules, no one had considered how to get wiring to these electrified components. Every wall in the building was concrete block (CMU) construction, meaning once door frames were set and block was laid around them, it became impossible to access the frames without demolition.
This problem was amplified by the aftermath of the 1999 Columbine shooting, which prompted schools nationwide to implement enhanced security and access control systems. The design and construction industry simply wasn’t prepared for this rapid shift in building requirements.
Makeshift Solutions (2003-2006)
Gary found himself “running around with a battery drill” trying to create pathways for wires before doors were set. He created spreadsheets and drawings to consolidate scattered information from hardware schedules, door schedules, and electrical and technology drawings.
“I’m drilling holes, you know, because these doors are gonna be set, and there’s no way to get to it,” Gary explained. “Every wall in this building was concrete block wall.”
The coordination challenges were immense. Electricians claimed they don’t do little wires, meaning low voltage.” No contractor took responsibility for the pathways to the devices on the frames. As Gary colorfully put it, “If I heard ‘this is not my job’ one more time, I was going to go crazy.” In response, Gary reached back to his supervisor, Ron Hicks, an experienced architect and Director of Construction Services for the firm. Gary and Ron had developed a great working relationship over the previous 8 years. “We came from two different sides of the fence, but we found a terrific comradery by focusing on solving problems in the field.” Ron offers. “Our backgrounds are so different, yet we see the business through the same lens. We remain colleagues and great friends to this day.”
The E-Frame Concept (2006-2019)
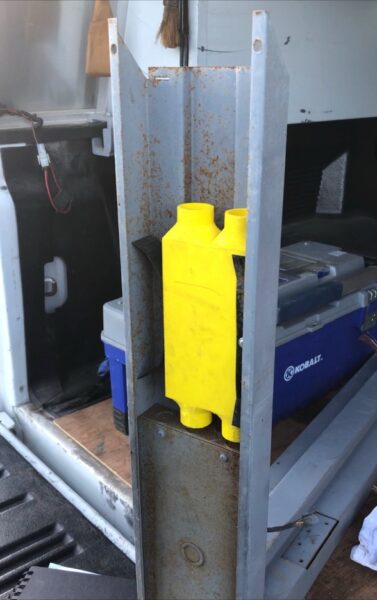
Following these difficult early experiences, the team developed what they called an “E-Frame” concept around 2006 – detailed drawings showing how conduit should be routed within door frames. This solution specified metal conduit and junction boxes configured in a way that would allow flexibility for different access control options.
“We started adding more details on our drawings and specs,” Ron Hicks, an experienced architect and co-inventor of Frame Frog explains. “It was our own little in-house term. It was a drawing of a frame, and it had conduit in the frame.”
The E-Frame design should have worked in theory, but implementation proved nearly impossible. They found only one local hollow metal shop willing to try their approach, which required creating a special bender to route conduit around frame corners.
“Hollow metal guys are like, ‘I don’t screw around with conduit in a frame. That’s not my problem,'” Ron recounts. When the one contractor did implement it correctly, “Our field reps are going, ‘this is awesome.’ The contractors are liking it, but it was so infrequent.”
The Product Breakthrough (November, 2018)
After years of frustration, a pivotal moment occurred in November 2018. Gary and Ron were sitting in an office “bemoaning the fact that we just keep pounding our head against the wall to get this stuff fixed.” Gary was approaching retirement, and the persistent problems still had no systematic solution.
The breakthrough idea was simple but profound: “What if we came up with a product that we could just sell that would get them to do what we want them to do?”
This marked the transition from a concept to a product. They identified five critical problems to solve:
- Creating a radius path for wiring around tight frame corners
- Enabling post-construction fishing of wires
- Providing funnels to guide fish tape when working blind
- Adding interior routing to direct fish tape to specific paths
- Eliminating the need to disassemble junction boxes for conduit connections
Product Development (2019)
The team initially created simple 3D printed prototypes in-house but quickly “went past the capacity of our architectural software to be able to make something that you could actually produce.”
They hired an industrial designer and went through approximately 20 iterations of the product design. A key innovation was the “funnel design” – when pushing fish tape into a box inside the frame blindly, the funnel would guide it to the proper conduit path.
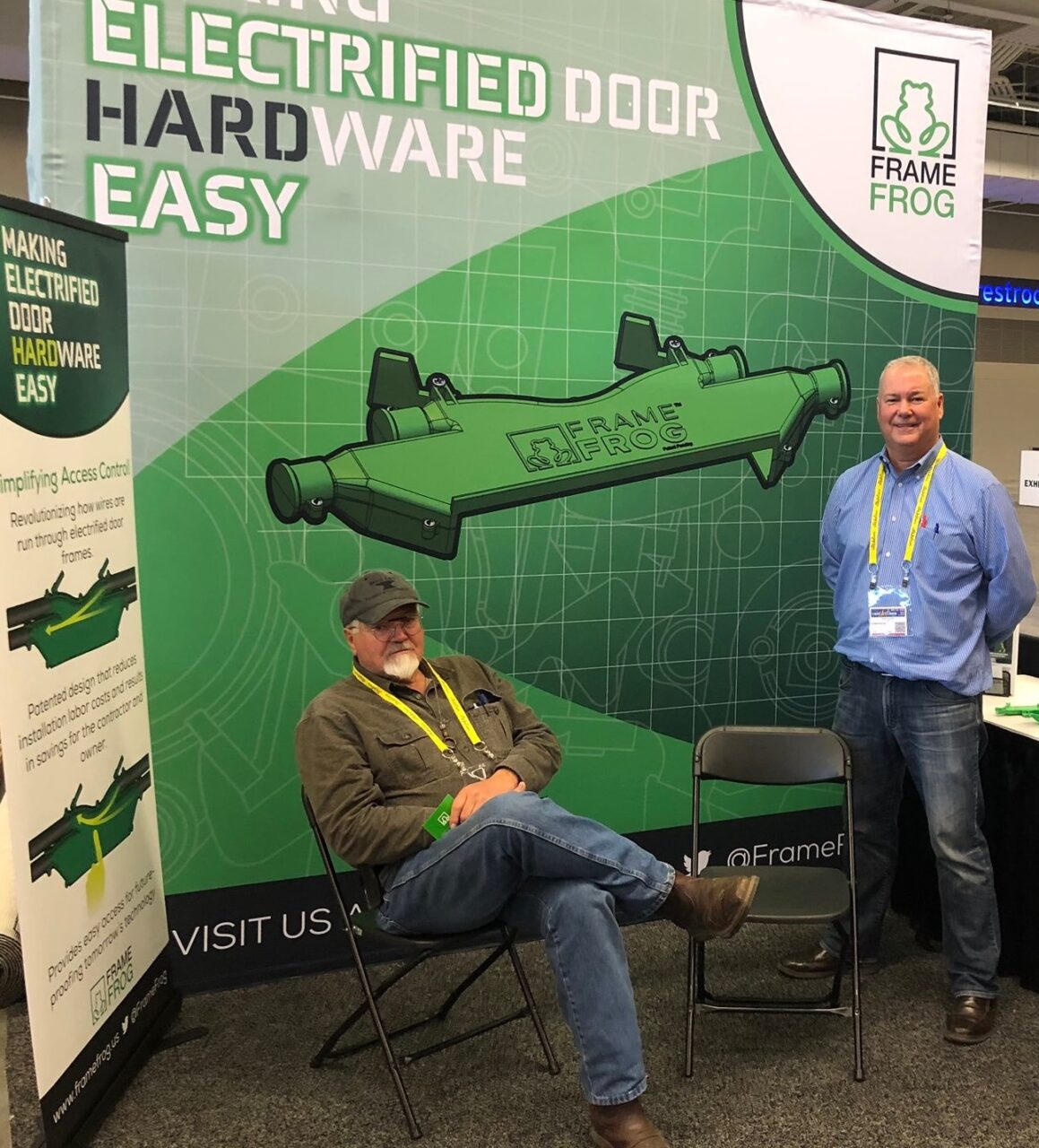
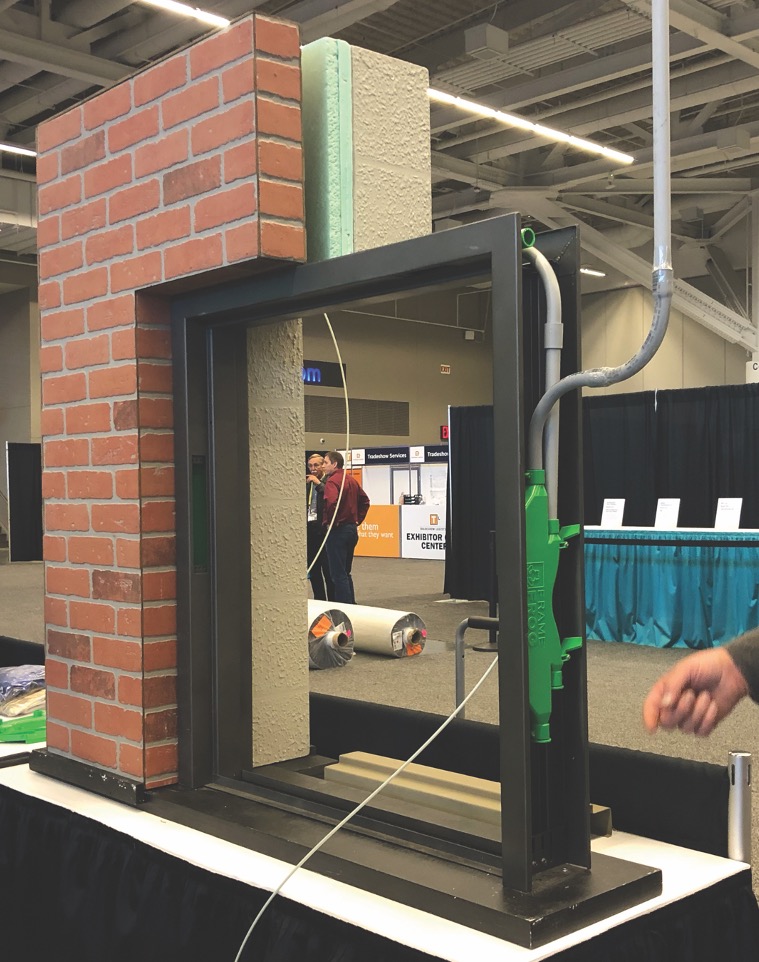
They also transitioned from metal components to ABS plastic boxes with PVC conduit, which could be joined with all-purpose glue, eliminating the complex assembly required with traditional metal boxes.
By late 2019, they had a finished product and a company willing to manufacture it. Their first shipment arrived just two weeks before their industry trade show debut at DHI in Cleveland, Ohio.
Frame Frog had evolved from a frustrating construction coordination problem into an elegant product solution that could be installed by “anybody with a screwdriver.” The journey took nearly two decades from problem identification to market-ready product, but the result was a solution to a persistent construction challenge that had plagued the industry since the early 2000s.
Frame Frog continues to ascend in the complex construction market, solving many coordination and installation problems on job sites across the US and Canada, as well as serving the facility for maintenance, repairs and upgrades to security systems for the life of the building. The future is looking bright.